Are Spreadsheets Dead Weight?
Shops often share their data management woes, so when I came across these five reasons for making the change from spreadsheets to a real-time, graphical job schedule, I just had to pass them along.
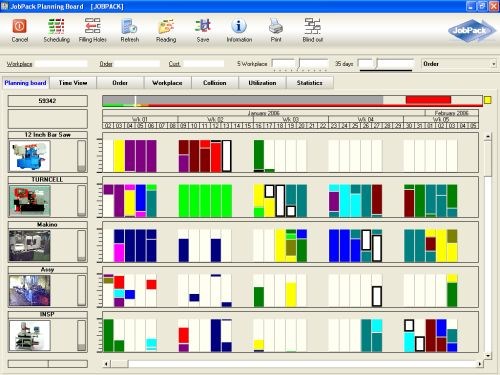
Shop Floor Automations thinks spreadsheets on shop floors are outdated and killing productivity. Here are their reasons why:
1. No ROI for time spent on spreadsheets. You are spending time manually noting information on a spreadsheet plus doing related administrative work, such as filing and searching for work order data info. If you have an operation with more than a couple of machines and more than a handful of employees, this is time wasted. You could instead have software with real-time insight from your production schedule that shows capacity usage and keeps jobs running on time.
2. Data entry errors require revisiting. Have you ever needed, or has an employee ever needed overtime approved to fix errors with spreadsheets? This is more time, resources and money spent fixing human errors. Instead, there is software that will help with data entry – for example, no duplication errors from entering work times. You will also have day-to-day planning data based on real-time capacity versus guesswork based on previous spreadsheets.
3. Control-F isn’t the answer. If you are looking for specific info in a spreadsheet, it is likely you need to remember data from a certain tab, or you go tab to tab and press good old “Control-F” to find the info you think you are looking for by keyword. You especially can’t use Control-F if you print all the spreadsheets and file them away, while never saving the digital copies (perhaps due to lack of storage space on an old computer). Instead, particular software programs can help access work orders and look at job statuses immediately without spending more time sifting through information.
4. You dread growth because it means more paperwork. A spreadsheet is not going to be able to adjust by itself when you get new jobs in, or when a job is canceled. A spreadsheet also isn’t going to tell you when there are issues with a machine causing a bottleneck. It’s especially a bad situation if you get a last minute rush order in from a big client and you feel like you have to turn it down because you don’t want to spend the time figuring out how to re-organize jobs. Job tracking, planning and scheduling combined into one simple interface will help your production run more efficiently and to meet, or surpass, promised due dates.
5. Machinists are not office clerks. There is a sizable skills gap in manufacturing that will be filled slowly over the next few years, and asking a qualified machinist to spend time helping with redundant paperwork that automated software could be doing for you is not in your best interest. They want to be able to get their hands dirty, create and contribute to a $2 Trillion Dollar, Made in America industry. Asking them to struggle with spreadsheets is an unfair thing to ask when their rare talents can be used elsewhere. User-friendly software only requires a few button pushes for operators to provide immediate feedback on current job statuses.
Related Content
-
How to Analyze and Optimize Cutting Conditions to Reduce Cycle Time
Plastic injection mold design and manufacturing company puts NC program optimization software module to the test. The results were surprising.
-
What is Scientific Maintenance? Part 2
Part two of this three-part series explains specific data that toolrooms must collect, analyze and use to truly advance to a scientific maintenance culture where you can measure real data and drive decisions.
-
How to Use Scientific Maintenance for More Accurate Mold and Part Troubleshooting
Discover how adopting scientific maintenance approaches helps improve mold lifespan, minimize failures, and optimize production outcomes.