Concurrent Technologies, Desktop Metal Advance 3D-Printed Sand-Casting Mold Technology
Through a U.S. DLA contract worth a potential $15 million, the project will further develop the science and engineering of 3D-printed sand-casting molds.
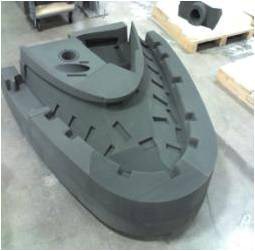
3D-printed, sand-casting molds. Photo Credit: DLA
The U.S. Defense Logistics Agency (DLA) has awarded Concurrent Technologies Corp. (CTC) a prime contract worth a potential $15 million to demonstrate the practicality of producing obsolete critical castings through 3D-printed sand-casting mold technology. In addition, the project will further develop the science and technology of 3D-printed sand-casting molds. CTC says it will work with subcontractor ExOne, a subsidiary of Desktop Metal, as well as the University of Northern Iowa, DLA and metal-casting foundries on the project.
“Several years ago, CTC recognized the need for a process to inexpensively and quickly produce obsolete critical castings needed by the Department of Defense [DoD]. The castings had been difficult to source because the original manufacturing designs, patterns and/or producers are no longer available,” Mike Tims, CTC advisor engineer and this program’s manager and principal investigator, says.
The base year of the contract is worth $4.6 million; four one-year options, if all exercised, would bring the total value of this effort to a potential $15 million. This project will demonstrate 3D-printed molds and cores for sand castings to the DLA supply chain and to foundries, which could then produce the castings that the industry is not currently positioned to make because traditional tooling is no longer available.
Digital casting is enabled by binder jet 3D printing technology. Replacement parts can be cast in tooling printed layer by layer in sand directly from a digital file without making physical patterns.
“Supply chain agility is a core advantage of 3D-printing technologies like binder jetting and digital casting, which allow low or high volumes to be produced efficiently and economically,” Ric Fulop, founder and CEO of Desktop Metal, notes. “We’re proud to partner with CTC in this project to address casting obsolescence 3D-printed sand molds to ensure defense readiness.”
This project builds on the expertise CTC has developed through 30+ years of advanced engineering and manufacturing, particularly through two Office of Naval Research projects that developed, used and implemented printed sand-casting molds.