3D Printing Systems Demonstrate Large-Scale Mold Building
CNC machine and large-scale large-scale additive manufacturing machine producer Thermwood highlights partner projects that advance mold production capabilities in the aerospace and defense industries.
Thermwood is a manufacturer of high-speed three- and five-axis machining centers for woodworking, aerospace, plastics and composites industries. The company has also evolved its expertise in large-scale additive manufacturing of thermoplastic composite molds, tooling, patterns and parts with its line of LSAM machines that 3D print and trim on the same machine. The company notes two successful mold applications with partner collaboration using this technology.
Thermwood cooperated with General Atomics to produce a CNC trim mold. Using a Thermwood LSAM 10' × 20', the tool was printed from ABS (20% carbon fiber-filled) in 16 hours. Total machining time was 32 hours. The final part weighed 1,190 lbs, and represented a cost savings of around $50,000 when compared to traditional methods. Total lead time for the part decreased from 6-8 weeks to less than two weeks. The resulting mold was suitable for large, deep 3D geometries, backup structures and vacuum piping.
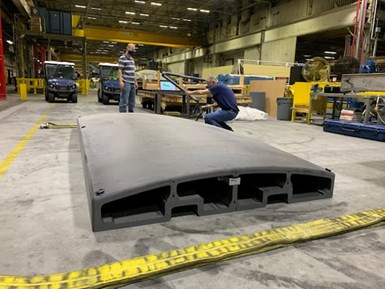
Stretch form production tool.
A collaborative effort between Spirit AeroSystems, Thermwood and Techmer PM produced what is believed to be the largest stretch form tool ever 3D printed, measuring 6.5' wide × 15' long. Like the one mentioned above, this project used the LSAM dual gantry print and trim system. Using carbon fiber-filled polycarbonate, the mold was printed into four different sections, two at a time, for a total print time of 29 hours and 20 minutes — cutting print time in half.
All surfaces of the parts except for the front working surface were then machined in place and the mating faces were machined flat. Draw bolt holes and slots were machined into the back of the tool to enable the parts to be bolted together in addition to the adhesive, and alignment holes and countersink holes were machined into the center sections of the tool.
Once alignment pins and brackets were installed, adhesive was applied to securely mate the mold sections together by hand. The final working surface measured within ±0.005", well within Spirit’s requirements.
Related Content
-
3D Printing Innovates Hot Runner Manifold Design
Metal 3D printing combined with a conventionally machined manifold block overcomes flow shadows on valve gates and offers faster color changes while providing closer system pitch centerlines between cavities.
-
MMT Chats: The Connection Between Additive Manufacturing Education and ROI
This MMT Chat continues the conversation with Action Mold and Machining, as two members of the Additive Manufacturing team dig a little deeper into AM education, AM’s return on investment and the facility and equipment requirements to implement AM properly.
-
A 3D Printing Retrospective
A personal review of the evolution of 3D printing in moldmaking throughout the past 25 years.