Replaceable Drill Tips Suitable for Aluminum and Non-Ferrous Materials
New SMDT-NAL drill tips from Sumitomo are coated with diamond-like Carbon DLC ‘Aurora’ Coating for two to three times higher feed rates.
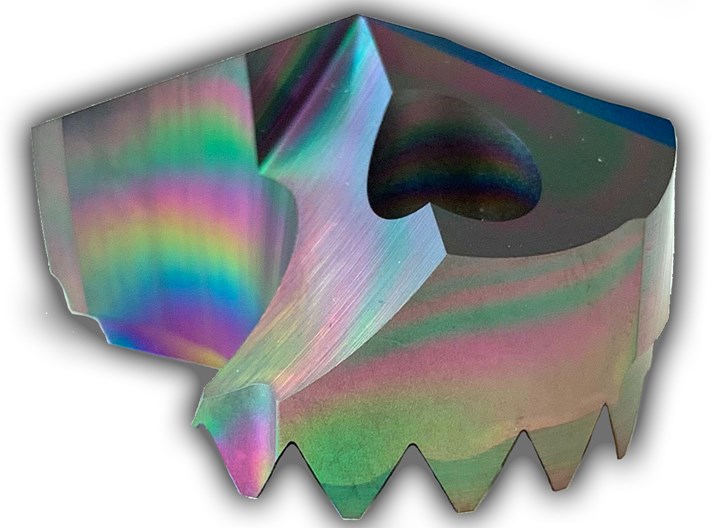
Photo Credit: Sumitomo Electric Carbide Inc.
Sumitomo is expanding its existing SMD Replaceable Tip Drilling line with new SMDT-NAL drill tips. SMDT-NAL features the proprietary diamond-like Carbon DLC ‘Aurora’ Coating. These replaceable drill tips are suitable for machining aluminum alloys and non-ferrous materials. SMD holders include deep-hole drilling up to 12 XD standard and the SMDT drill tip lineup offers diameters ranging from fractional sizes 15/32 to 11/4.
DLC ‘Aurora’ Coating is an amorphous film mainly composed of carbon with lubricity and chemical stability. It is said to feature high hardness, superior tribology properties and excellent adhesion resistance. DLC films are used as a coating for cutting tools for aluminum alloys.
Sumitomo is committed to developing new tools for the automotive, aerospace and energy industries. Replaceable tip drilling (SMDT-NAL), solid carbide drilling with DLC coating (MDW-NHGS) and DLC-coated indexable
inserts (WDX) round out the lineup for aluminum holemaking.
Key benefits of these products include the smooth coating surface, which results in stable chip evacuation; the aluminum welding resistance; a hardness of 60 GPa for abrasion resistance and increased penetration rates caused by low friction coefficient. All these benefits allow users to machine with two to three times higher feed rates than uncoated drills, according to Sumitomo.
Related Content
-
Ten Things You Need to Know about Circle Segment Milling
Considerations for evaluating if circle segment end mills or conical barrel cutters are right for your mold machining applications.
-
Cutting Tools: Technology to Make Your Process Easier
Having the right cutting tool technology for moldmaking is a crucial component for efficiency and cost-effectiveness.
-
Precision Meets Innovation at IMTS 2024
After attending IMTS, it's clear that the integration of advanced technologies is ready to enhance precision, efficiency and automation in mold manufacturing processes. It’s a massive event, so here’s a glimpse of what the MMT team experienced firsthand.