Cost-Effective Thread Former Reduced Torque
Walter introduces the TC410 advance HSS-E thread former, a versatile new TiN coated threading tool that can be used universally for blind and through-hole threads in most materials.
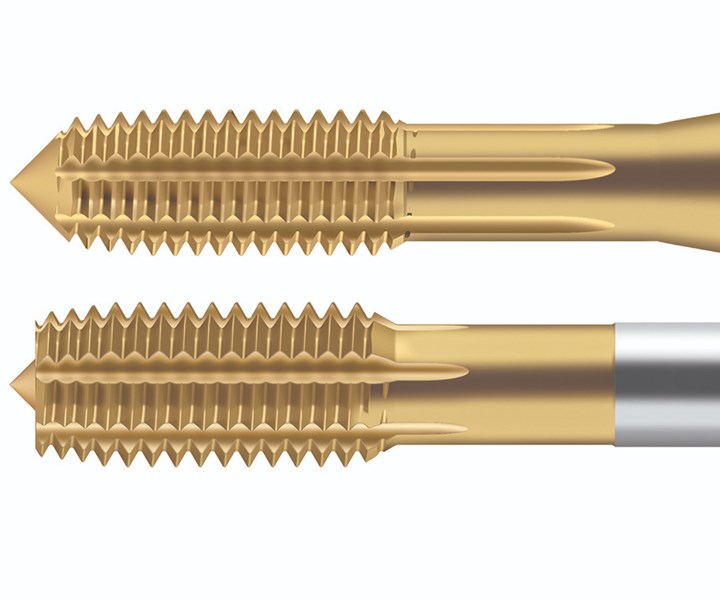
Walter introduces the TC410 advance HSS-E thread former, a versatile new TiN coated threading tool that’s cost-effective, even for small and medium batch sizes. It can be used universally for blind and through-hole threads in most materials having a primary application in ISO material groups P, M and N and ISO K and S as a secondary application.
Key advantages for using the thread former are superior performance, reduced torque and longer tool life thanks to new geometry and a post-treatment after the coating process. The post-treatment provides an extremely smooth surface on the tool. Having a smooth surface reduces friction between the tool and the workpiece and consequently the amount of heat generated. Minimizing the production of heat reduces wear and thus increases the useful life of the tool.
The thread former is offered in two variants: With lubrication grooves for applications that need help getting coolant to the area where the forming is happening or without lubrication grooves for when the coolant is already pooled in the hole. Deeper threads can be produced in certain materials with these tools. Also offered are a wide variety of configurations covering thread styles, thread tolerances and shank standards, including an option for LH threads.
Its excellent price/performance ratio makes the TC410 Advance an attractive choice for users with medium to large batch sizes. This is because it can produce more threads with the same tool at a reasonable price. With its combination of productivity and cost saving features the new tool will find ready application in the automotive and energy industries along with general metalworking.
Related Content
-
Moldmakers Deserve a Total Production Solution
Stability, spindle speed and software are essential consideration for your moldmaking machine tool.
-
The Ins and Outs of Hot Runner Temperature Control
A training checklist that explains the why and how of proper hot runner temperature control and system management.
-
Solving Mold Alignment Problems with the Right Alignment Lock
Correct alignment lock selection can reduce maintenance costs and molding downtime, as well as increase part quality over the mold’s entire life.