The Designer's Edge: Your Shut-Down Procedure
Randy continues his look at rust when it comes to mold cleaning and maintenance with a review of a solid shut-down procedure.
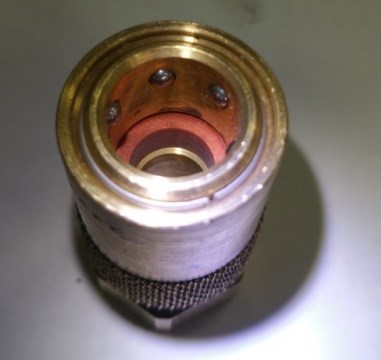
Water connection coupler.
Don’t underestimate the value of a good shut-down procedure when it comes to rust issues. When running a mold on a chiller you are at risk for rust issues due to condensation, if shut-down is not done properly. When the mold is done running or going to sit idle, it should be brought up to room temperature and then have a protectant immediately applied. From a tool maintenance perspective, I recommend staying away from chillers. In some cases, chillers are used because the tool does not have adequate cooling designed in it.
Maintaining the water connections and o-rings is another area to consider. Water connections should be observed for leaks at PMs. Then if any leaks are observed in production, it should be addressed as soon as possible.
O-rings in the water connections will fail over time. Typically, most do not have a procedure for replacement, so the first evidence of a bad o-ring is a leak. Also when running molds with higher water temperatures (above 180 degrees), the water lines should be hard plumbed using fittings with a tapered surface to seal. As opposed to the standard water coupler connection using o-rings. This will reduce the chance of an injury with a water leak using high temperatures.
With internal o-rings l recommend replacement at every preventive maintenance to prevent issues. One thing a toolmaker does not like are components or cavity inserts being corroded with rust, these can be very difficult to remove when rusted.
Being in charge and/or maintaining tools in manufacturing, has taught me to address these issues promptly. Sometimes, by running hours of scrap after a preventive maintenance. Preventative maintenance meaning when the mold is completely disassembled, cleaned and new lubricants applied. I have found that some greases are more prone to cause bleeding if not applied properly and others to do not hold up well at high temperatures with high mechanical friction.
I have tried numerous greases on the market and not one covers all aspects and applications, but it is critical to find the right grease for your application to reduce issues and failures. It is also important to make sure your components are designed properly, using proper coatings and hardnesses to reduce failures. It is not always the lubricant at the root cause of mechanical failures.
In some cases greaseless tools are a necessity, which can achieve good maintenance results if properly designed and components are coated. Typically, for high volume tools I spec 100,000 cycles between PMs for most materials and tools, but with higher temperatures and glass-filled materials I set the spec at 50,000 cycles. However, there are always cases where those cycle counts are too high.
Read Next
New Blog Series: The Designer's Edge
Here's to a new year and a new bi-weekly blog series by guest blogger Randy Kerkstra that will offer ways to design and use the mold for effective troubleshooting and for yielding the largest processing window possible. We appreciate Randy's willingness to share his passion for solving problems and lessons learned throughout his 27 years in mold building and molding. We hope this series begins an ongoing dialogue on how mold shops can have a bigger impact on the molding process.
Read MoreHow to Use Strategic Planning Tools, Data to Manage the Human Side of Business
Q&A with Marion Wells, MMT EAB member and founder of Human Asset Management.
Read MoreAre You a Moldmaker Considering 3D Printing? Consider the 3D Printing Workshop at NPE2024
Presentations will cover 3D printing for mold tooling, material innovation, product development, bridge production and full-scale, high-volume additive manufacturing.
Read More