The Designer's Edge: Slide Lock Angles
Slide lock angles are prone to wear if they are not maintained properly because their surface experiences a lot of mechanical friction during mold close. Randy shares pointers for avoiding this wear.
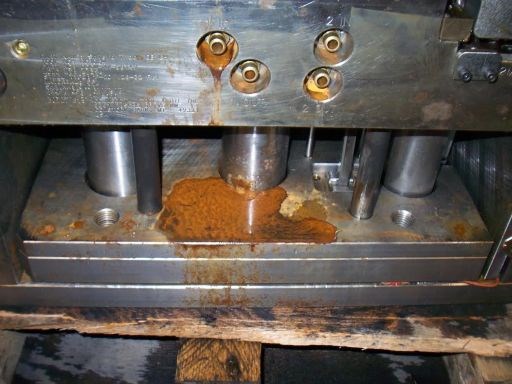
This photo shows rust on the exterior of a mold that was a result of improper tool shutdown, which left water in the lines.
Slide lock angles are other components prone to wear if they are not maintained properly. This is because their surface experiences a lot of mechanical friction during mold close. Many people will focus on greasing the slide's horn/guide pin, and although this does need to be greased it is the lock angle surface that really needs to be the focus. Once the lock angle surface wears, it can contribute to flash with loss of preload.
Many moldmakers apply more grease than necessary. Whenever cleaning the parting lines or cavity surface, mold cleaner should never be sprayed directly on the components or the cavity surface that has lifters or ejector pins. This can create bigger issues with bleeding on the plastic part and loss of lubricant on the component. If you need to remove excessive grease from a component, clean with a rag sprayed with mold cleaner. Proper PM methods and applications using the proper grease will reduce startup issues with scrap parts.
A few years ago I had bleeding issues with some molds I was running for a customer. They wanted to come in and show us how to apply the grease properly. I thought to myself, "Right, I’ve been doing this for years." However, I kept an open mind and actually learned something about proper grease application, which then had a huge impact on startup scrap.
Another area that varies from molder to molder is the maintenance of the mold's exterior. This does not take much effort and will protect your press platens. The outside side of the tool, specifically the clamping surfaces, should be cleaned after pulling and a rust preventative should be applied. This should also be performed on the platen surfaces. The other exterior surfaces of the mold should also be examined for water leaks or rust, and cleaned up or sent to the toolroom for investigation of the water leak. The mold-mounting surfaces should also be examined for burrs or dings during PM and when setting or pulling the tool.
Next month I will begin a series on repairs in the press.