Designing Molds, Building Futures
Wes Cobb, president of Technical Design Associates Inc. in Brevard, North Carolina, is the Society of Plastics Engineers (SPE) Mold Technologies Division’s 2016 Mold Designer of the Year.
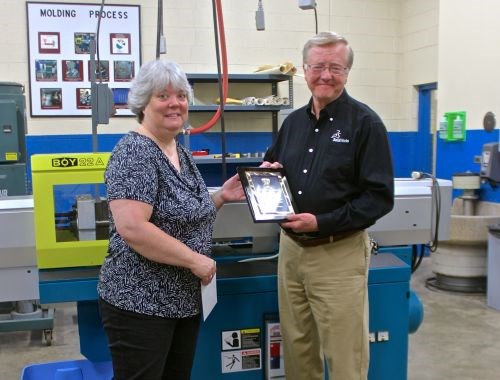
Brenda Clark, on behalf of the SPE Mold Technologies Division, presents a plaque and $500 honorarium to Wes Cobb to mark his being named the 2016 Mold Designer of the Year. Clark made the presentation at AB Tech, a community college in Asheville, North Carolina, whose SolidWorks training program Cobb chose to receive the $500.
Wes Cobb has made an indelible impression on the lives of many mold designers. He’s mentored them and has given of his time and experience to AB Tech Community College’s Engineering and Applied Technology program to ensure that young people desiring a rewarding career in the industry will not left to fend for themselves.
Wes Cobb, president of Technical Design Associates Inc. in Brevard, North Carolina, is the Society of Plastics Engineers (SPE) Mold Technologies Division’s 2016 Mold Designer of the Year. Just as the SPE recognizes leaders in moldmaking who have made a difference like this year’s Mold Maker of the Year Geoff Luther (see my blog from July 18), the division also honors a leading mold designer who has accomplished much in his or her career and given back to the industry, too.
Cobb was nominated by Brenda Clark, engineering manager for Hasco America Inc. “Wes was instrumental in assisting many young and upcoming mold designers in North Carolina. He even brought me down to North Carolina from Connecticut, giving me the opportunity to get on the computer and further my mold design career,” she says.
Cobb started out as a drafter for the Taylor Instrument Co. in Rochester, New York, in 1966. Then, following a four-year stint in the U.S. Air Force, he joined Alliance Mold Co., also in Rochester, as a mold designer trainee in 1972. Cobb says that this training combined with seven years of higher education is what launched him into a mold designer role at Eastman Kodak in 1976. Three years later Cobb had the opportunity to relocate to North Carolina where he continued to design molds and products until he was hired in 1981 as the first engineering manager for Atlas Tool and Mold in Arden, North Carolina, a position he held until he broke out on his own in 1989 and opened Technical Design Associates.
“He has designed many molds from unscrewing to over-molding and hot runner designs in the 27 years of running his own business,” Clark says. “These are too numerous to list, and they cover a wide range of products and industries for plastics. I worked for Wes between 1992 and 1994, before my children came along. We worked many long hours and created many designs.”
Clark says that in addition to his mold design work, Cobb also was instrumental in starting the apprentice program for mold making and mold design at AB Tech in the late 1980's, and he started and led the local SolidWorks Chapter for many years. In fact, Cobb has designated AB Tech’s Solidworks training program as the beneficiary of the $500 honorarium that comes with his Mold Designer of the Year award from SPE’s Mold Technologies Division.
“I am truly so pleased and proud to be recognized in this way,” Cobb said when he was notified that he was chosen to be honored. “It’s all just starting to sink in. This business has definitely had its ups and downs, but the people I’ve had the good fortune to work with over the years have made it worthwhile for me. I reluctantly had given Brenda some background information thinking she might be wasting her time. I thought my contributions to the industry were not close to being on the scale of those people who had mentored me while never receiving any recognition in their careers for their efforts.”
For me, Cobb’s humble gratitude is what sweetens this awards program. It’s a privilege to be able to meet and recognize those who go out there every day, doing what they love, and sharing that passion with others without a thought of what they might get in return. Wes Cobb is a mold designer, but he is also very much a builder of futures within our industry. Congratulations, Wes.
Related Content
From Injection Mold Venting to Runnerless Micro Molds: MMT's Top-Viewed June Content
The MoldMaking Technology team has compiled a list of the top-viewed June content based on analytics. This month, we covered an array of topics including injection mold venting, business strategies and runnerless micro molds. Take a look at what you might have missed!
Read More30 Under 30: The New Face of Moldmaking
Young professionals are vital to the moldmaking industry, and it is important to acknowledge those making strides in shaping the industry's future. MoldMaking Technology recognizes the industry's young talent through its inaugural 30-Under-30 Honors Program.
Read MoreLeading Mold Manufacturers Share Best Practices for Improving Efficiency
Precise Tooling Solutions, X-Cell Tool and Mold, M&M Tool and Mold, Ameritech Die & Mold, and Cavalier Tool & Manufacturing, sit down for a fast-paced Q&A focused on strategies for improving efficiencies across their operations.
Read MoreThe Role of Social Media in Manufacturing
Charles Daniels CFO of Wepco Plastics shares insights on the role of social media in manufacturing, how to improve the “business” side of a small mold shop and continually developing culture.
Read MoreRead Next
Reasons to Use Fiber Lasers for Mold Cleaning
Fiber lasers offer a simplicity, speed, control and portability, minimizing mold cleaning risks.
Read MoreHow to Use Continuing Education to Remain Competitive in Moldmaking
Continued training helps moldmakers make tooling decisions and properly use the latest cutting tool to efficiently machine high-quality molds.
Read MoreHow to Use Strategic Planning Tools, Data to Manage the Human Side of Business
Q&A with Marion Wells, MMT EAB member and founder of Human Asset Management.
Read More